
At the request of the member companies and with guidance and support from the Defense Advanced Research Projects Agency (DARPA), the MEMS Industry Group engaged in a comprehensive effort to understand the realities and perceptions about the reliability of MEMS: from analyzing available data with successes and challenges, to establishing information exchange channels and to defining a coherent strategy for reducing reliability-related barriers in the development of new MEMS products. The activities to address MEMS device reliability and accelerated life test consisted of two surveys and a series of working group discussions in two annual conferences in which MIG member companies participated. The first survey and conference took place in 2003 and were designed to address the issues of MEMS product reliability in general. The second survey and conference took place in 2004 and provided an updated assessment of MEMS reliability status, as well as a focus on accelerated lifetime testing for MEMS product development. While the surveys provided the state of MEMS reliability and ALT in the industry, the MIG conferences, METRIC (MEMS Technology Roadmap and Industry Congress) 2003 on Reliability1 and METRIC 2004 on ALT,2 were the events where the MIG members debated and analyzed the issue at hand and proposed short- and long-term actions.
Survey Highlights
The initial portion of the survey questions was set to establish the type of MEMS company and to define the categories of the MEMS devices involved. This was followed by the expectation, perception and state of the respondent’s product lifetime, reliability issues, failure investigation and accelerated life testing. Lastly, the questionnaire inquired about the needs of the survey participants. The following is a synopsis of the survey highlights:
- The survey shows equal numbers of respondents working with sensors versus actuators, primarily in hermetic packaging. The majority indicated they required their devices to have lifetimes of at least 10 years. The number of defective units permitted depends largely on the customer and the operating environment.
Reliability Demonstration
The reliability of MEMS is still a subject of interest and discussion. MEMS products such as accelerometers, pressure sensors and inkjet nozzles have proven to be tremendously reliable. On the other hand, some products are still on the design board, unable to convince their potential customers of their reliability. In the 1960s, electrical components emerged as replacements for mechanical devices. Technology development is now at a stage where micromechanical devices are poised to replace electrical devices. In the 1960s, electrical components were also promoted as much more reliable devices than their mechanical counterparts. A primary goal for MEMS is to prove that they are equally or more reliable than their electrical counterparts. As MEMS devices continue to mature and enter more mainstream applications, these important reliability issues need to be better understood. The primary findings indicate that MEMS devices must demonstrate their reliability. This is a key step towards the education of any approval agencies as well as prospective customers.
Over 90 percent of the respondents indicated that customers require a demonstration of reliability. Of those respondents, however, only half have actually demonstrated the reliability of their respective MEMS device. This is not a reflection on MEMS reliability, but rather a reflection of the stage of the industry development or the MEMS device itself. Today, there are several examples of high volume MEMS devices (sensors and actuators) that have demonstrated high degrees of reliability with long product lifetimes.
Failure Modes and Acceleration Factors
One of the main challenges for MEMS devices involves the identification of optimum types of reliability tests to be performed and identification of the types of failure modes to expect. Based on these failure modes categories, reliability tests can be developed to test the device to failure. In this approach, tests are performed at stress levels beyond the product specifications. To gain insight from the survey respondents, they were presented with a choice of failure modes to vote on:
Charge Accumulation, Electric Short/Open, Clogging, Stiction, Contamination, Passivation, Crack Propagation, Delamination, Leakage, Micro Weld, Surface Modification, Temperature, Creep, Outgassing, Wear, Deformation and Package Stress.
Failure modes were both device- and package-specific. Packaging technology is paramount in providing for a highly reliable MEMS device. Many MEMS devices are typically protected from their environment by enclosure in a hermetically sealed package. The stress induced by the package can affect MEMS performance. Therefore, the integrity of the package over the life of the product directly affects the reliability of the MEMS device. It is no coincidence that the most successful MEMS devices, utilized today in high volume applications, have been able to employ more conventional packaging for hermetic sealing.
Table 1 lists the top five failure modes by MEMS device type chosen by the respondents. These failure modes manifest themselves during the manufacturing ramp process and are related to large volume production. Thus, these are failure modes that may not be apparent in the lab, but are noticeable and problematic when larger volumes of MEMS devices are fabricated during the start of production.

The majority of actuator devices have moving parts with contact. Thus, the top two failure modes for actuators are stiction and wear — two failure modes that deal directly with contacting surfaces. The majority of sensors in this survey, on the other hand, consist of moving parts without contact. Thus, electrical or package induced failures are the primary failure modes for these types of MEMS devices. As the variety of failure modes are investigated during reliability testing, some tests provide easy identification of these failure modes whereas others do not. Tables 2 and 3 list the top and bottom five failure modes in ease of identification, respectively. Wear, for instance, is considered a difficult failure mode to identify for actuators (moving parts with contact). Testing techniques such as chemical analysis, surface topography, force microscopy, and electron and optical imaging are not always successful in identifying the wear of a surface. One source of understanding stiction- or wear-related failures is the MEMS element itself. In these cases, high frequency modulation of the MEMS element provides an excellent avenue towards understanding these types of contact failures.


The respondents also provided input on their ability to accelerate these failure modes through identifiable tests. The ability to accelerate these tests is provided in Table 4 by rank, in order of “Most Able to Accelerate” to “Least Able to Accelerate.”

There are a number of reliability tests and acceleration factors used to identify these failure modes. There are instances where specific stress tests can accelerate a number of failure modes. The overall number of acceleration factors utilized to identify a specific failure mode is shown in Figure 1. It is up to the MEMS developer to determine which types of acceleration factors are best for working with a specific failure mode. Despite the number of acceleration factors shown in the preceding chart, only half the respondents indicated they have identified the proper acceleration factors to assess the lifetime of their respective MEMS products.

Fig. 1 Acceleration factors for specific failure modes.
Many of the package-related failure modes can be accelerated, using a suite of military specification tests utilized by the semiconductor industry. These tests are an excellent resource for developing a reliability plan for a new MEMS device. During reliability testing, it is sometimes impractical to test a device for a long period of time to demonstrate reliability. For instance, operating a device for ten years is not feasible. Thus, the MEMS device designer or manufacturer needs to identify a number of acceleration factors for each failure mode. Temperature is the most common acceleration factor. Typical temperature acceleration factors consist of thermal shock, thermal cycles, hot and cold storage, and high and low temperature operation.
Failure Identification and ALT
Failure modes and their respective mechanisms can be identified in a number of ways. This identification can consist of a simple 1x visual inspection, to a semi-destructive method using a scanning electron microscope (SEM). Figure 2 is a list of the top failure detection techniques. The top two techniques from this table are non-destructive. These two techniques rely on device parametric performance — mechanical and electrical. In other words, the device itself is providing the test feedback on whether it has passed or failed a particular test.

Fig. 2 Failure detection methods.
Over 60 percent of the respondents indicate they have a built-in test feature to make sure their device is functioning properly. The vast majority of survey respondents (76 percent) indicate they cannot tie a particular ALT technique to a particular failure mode or failure mechanism. While 68 percent have identified the failure mechanism of their device, 67 percent have an incomplete understanding of this failure mechanism. This implies that although these MEMS companies have identified a failure mechanism, they do not necessarily know how to fix it.
Over 70 percent of the survey’s respondents perform accelerated lifetime testing. The majority of these ALTs (> 50 percent) are custom tests. In other words, the MEMS designer had to develop custom tests to meet the customer-driven requirements, while addressing potential failure modes. It is common for the MEMS designer to invent new methods for testing the MEMS-specific functions. In some cases, these new methods are modified or adopted from macro-machine tests.
A difficult area for most respondents is the degree to which MEMS customers and suppliers understand the ALTs and their respective failure mechanisms. Figure 3 depicts what the MEMS designers and suppliers see as the most important ALT issues to resolve. Thus, the top two issues involve a better understanding of the acceleration factors, failure modes and failure mechanisms.
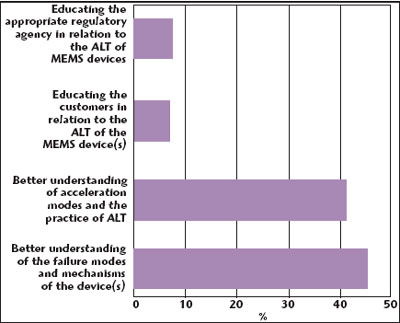
Fig. 3 Important ALT issues to resolve.
Concluding Remarks
Commercialization is critical for MEMS to mature as a technology. As MEMS devices are deployed in many configurations where incumbent components are still in use, it is imperative that the reliability and lifetime expectations are met or exceeded. The expected lifetimes of MEMS devices is very similar to those of typical electrical components — in most cases, lifetimes greater than 10 years is expected. Thus, the reliability requirements for MEMS devices are equal to or more stringent than for their electrical counterparts. The most influential means for educating the MEMS customer is by demonstrating that devices can successfully pass similar reliability tests. Since MEMS packaging is critical to the function of the MEMS device, reliability tests need to be tailored to address both the device and packaging potential failure modes.
With the history of the successful manufacture of high volume, commercially available MEMS devices, it is important to ensure high levels of communication with future customers and the various reliability regulators about the reliability successes of these MEMS devices. There is more than adequate proof that MEMS devices have achieved high reliability goals with lifetimes in excess of 10 years.
The main objective of accelerated lifetime testing is to uncover and understand the failure mechanisms of a device in a relatively short period of time. Many MEMS devices undergo standard ALT and reliability tests. Borrowing from the practices of the semiconductor industry as well as other related industries (such as macro-machines) is always an excellent first step for ALT. However, a majority of MEMS designers and suppliers are developing custom MEMS tests to meet the needs of their customer requirements. The caveat is that MEMS issues such as hermeticity and package-related stress may limit which of the semiconductor industry practices can realistically be adopted. It was exciting to learn that many MEMS devices are making use of wafer-level packaging techniques. The yield improvements and cost savings of these types of packages is an excellent benefit and shows that the maturity of MEMS devices is improving.
Based on the survey of MEMS package types, reliability and ALT testing can also leverage existing specifications as defined in Mil-Std-883. As with any reliability and ALT plan, these need to be driven by the customer’s requirements. The majority of the survey respondents indicates the customer and the reliability as the drivers. Even the reliability failures are clearly defined in terms of not meeting a particular customer specification.
MEMS devices that involve moving parts with contacts or sliding friction can have failure modes that are most challenging to resolve. Reliability testing using temperature, voltage and frequency of operation are some of the top acceleration factors in resolving the identified failure mode. Most of the survey respondents indicate that they are challenged by tying a particular ALT to a certain failure mode as well as by understanding the failure mechanism. In these cases, a number of acceleration factors will have to be utilized in order to help identify the failure mechanism and associated acceleration model in a relatively short period of time. This is what MIG hopes to accomplish with the surveys and its METRIC conferences — how to share the reliability and ALT knowledge among the member companies, so each can learn from one another to help the MEMS industry overall.
Acknowledgments
Thanks to Karen Lightman, Monica Takacs, Dr. Cleopatra Cabuz and the members of the MIG Advisory Group for their contributions to this project. The participation of the survey respondents and of the MIG member companies is greatly appreciated. This work is supported by DARPA under the DARPA/MTO program.
References
1. The METRIC 2003 Conference on MEMS Reliability, Annual Conference of the MEMS Industry Group Member Companies, Pittsburgh, PA, September 18–19, 2003.
2. The METRIC 2004 Conference on Accelerated Lifetime Testing, Annual Conference of the MEMS Industry Group Member Companies, Pittsburgh, PA, September 29–30, 2004.