The outstanding fabrication tolerances and scalability of IC processes have made MMICs the technology of choice for nearly all planar microwave components, including amplifiers, mixers, switches, oscillators—even fully integrated transceivers. However, fixed filters have been untouched by the MMIC revolution due to outdated assumptions about performance and availability. In this article, we examine the filter landscape and explain why MMIC should be the technology platform of choice for many filter applications.
RF consumer markets have rapidly evolved over the last 10 to 15 years to offer enhanced data rates and connectivity while also supporting ever-increasing numbers of users and connected devices. A similar market evolution is taking place in the aerospace and defense, test and measurement and “new space” markets, where increased amounts of high frequency content are being processed and manipulated across significantly more users. Next-generation systems will increasingly support multichannel, multiband and multiple emitter architectures to improve performance and offer the ability to enable multipurpose missions, at the expense of a massive increase in overall channel count and total bandwidth. These channel counts are supported by high speed data converters, which enable high instantaneous bandwidth for both traditional super heterodyne and direct conversion receivers. The effect of increasing analog-to-digital converter (ADC) bandwidth is illustrated in Figure 1, which shows the changing filter requirements as more signal processing is performed digitally. Increasing ADC sampling rates enables narrowband filters to be implemented digitally, but the increasing channel count makes filter size more critical. These trends place incredible strain on the physical packaging of a particular solution, with the expectation that more channels and processing power be supported within the same, or sometimes smaller, footprints.

Figure 1 Traditional superheterodyne receiver (a), superheterodyne receiver with digital down-conversion after the first IF stage (b) and direct conversion receiver (c).
To support higher channel density, component solutions have generally followed an evolution that emphasizes smaller size and higher frequency. Additionally, many system blocks and sub-blocks have been combined through the development of single chip integrated solutions (typically Si ICs), through the novel packaging of multiple chips within a single package (called multi-chip modules) or through some combination of both Si and non-Si ICs inside the same package (usually referred to as “heterogeneous integration”). No doubt these trends will continue for the foreseeable future, and innovations will be necessary to further reduce the physical size of high frequency hardware.
Filters are commonly used to provide channel or band selection and to clean up the spurious and unwanted signals or noise present in an analog signal chain. When it comes to miniaturization and improved channel density, filters are problematic because they consume much of a system’s overall footprint. Given their ubiquity, it is curious to consider why filters remain the least evolved block in the system diagram. They often lack tunability or reconfigurability, they are rarely integrated into a larger function block or package, they take up massive amounts of area and volume, they are susceptible to process variation causing lot-to-lot variability and they are often designed “in-house”—taking up valuable RF design resources.
The demands on space and size have forced a reassessment of the performance tradeoffs of future filter solutions. The emerging trend is toward prioritizing reduced SWaP, scalability and rapid custom filter development over the traditional preferences of low loss (i.e., high Q-factor), high out-of-band rejection and high power. As converter bandwidths increase and more signal processing is performed digitally, less signal processing is required in the analog domain. Less processing means fewer converter stages—therefore, fewer spurs spaced farther apart. Some filter metrics, such as insertion loss for channel selection filters will always be important, but size, scalability and development time are becoming more dominant concerns for system architects.
A key challenge for high performance systems is that filters are typically custom designs based on the system frequency plan or some unique coexistence requirements. This creates a challenge when building a business case for low volume opportunities because costs cannot be offset by multiple customers. Further, filters are often needed immediately, as they are added or changed to solve a specific issue arising during development. This makes a rapid, reasonably priced, first-pass design success approach essential to solving a particular custom filter request.
Considering the above, we contend that future competitive filter technologies must satisfy the following critical metrics:
- Extremely small—at least 2× smaller than existing solutions and the smaller the better
- Rapid development cycle with modest cost and a first-pass success design flow
- Scalable, highly repeatable manufacturing approach
- Acceptable performance tradeoffs among insertion loss, filter order, rejection skirt, etc. to enable size reduction to meet the system need
- Operation from low GHz to > 100 GHz to support all high frequency needs and preferably in a surface-mount package.
COMPARING FILTER TECHNOLOGIES
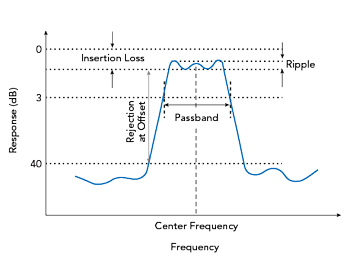
Figure 2 Performance metrics of a microwave filter.
No one filter technology is ideal for all applications, and no one performance metric defines a filter technology (see Figure 2). Performing a general comparison of filter technologies is complicated because a filter design can be a tradeoff among many parameters. While Q is important for a given design, there is no single figure of merit to predict how well a filter technology will meet a specification.